How to Choose Ring Die Pellet Mill Compression Ratio
When the raw materials are mixtures of a variety of materials, such as 50% grains and cottonseed with 50% agricultural waste, what are the requirements for moulding? Does the compression ratio need adjusting?
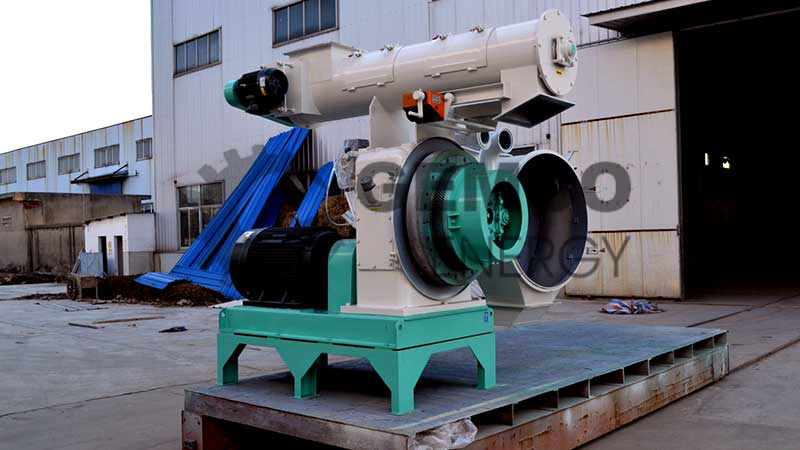
The compression ratio of the ring mode is the ratio of the effective working length of the ring mode to the diameter of the pellet press die hole.
The compression ratio of the ring mold of the ring die pellet mill can be selected according to the raw material formula and product requirements. Low compression ratio can increase output, reduce energy consumption and reduce the wear of ring die pellet mill spare parts. But the pellets will be loose, the length of the pellets will be different, the feed pulverization rate will be high. On the other hand, if the compression ratio of the ring die pellet mill ring mode, the pellets will be strong, smooth and glossy, and the pulverization rate will be low, but the cost of production will be high.
Pellet mill die of ring die pellet mill is generally made of carbon steel, alloy structural steel or stainless steel.
The material of the ring mould can be selected according to the corrosion of the material and the working strength of the ring die. For corrosive materials and ring mold which has very small pellet mill die holes, generally choose stainless steel. After the ring mold is used for several hours, the material friction causes the original inherent aperture to increase. Under the condition of constant effective compression length, smaller compression ratio, constant material and steam, the hardness of the feed is gradually reduced and the annular mold will be scrapped.
For different materials, different compression ratio should be selected.

The diameter of the pellet mill die is closely related to the diameter of the pellets and the composition of the raw material. The standard number in the ring die pellet mill industry is 8mm / 6mm / 8mm / 10mm, which is called conventional data. More than 10mm is hetertypic data, and the pressure needed for forming sawdust pellets should be larger if the pellet mill die hole diameter that larger 12mm, and the wear is also relatively large. Users generally call it sawdust bar making machine or bar making machine.
The thickness of ring die pellet mill die of wood chip pellets is very important for raw material forming.
If the die is too thick, the forming time of raw material will be longer, the density of wood pellets will be relatively large, and the extrusion difficulty will be high. The mould is thin and easy to fracture, the density of particles is relatively small, the extrusion temperature is low, the production is higher, but the molding rate is lower. The abrasive compression ratio of sawdust ring die pellet mill is determined by raw material, so let's give a few simple examples.
The compression ratio of poplar is 1: 6, the compression ratio of pine is 1: 7, the compression ratio of hardwood is 1: 5, and the compression ratio of chopped wood is 1: 5. The compression ratio of corn straw is 1: 8.
From these simple figures, the compression ratio of different raw materials is different. The harder the raw material is, the smaller compression ratio will be, the more puffy the raw material the bigger compression ratio will be, that is, the more fluffy the raw material is, the easier it is to be pressed. The fluffy raw materials contain more fibers, this kind of materials are easy to form.
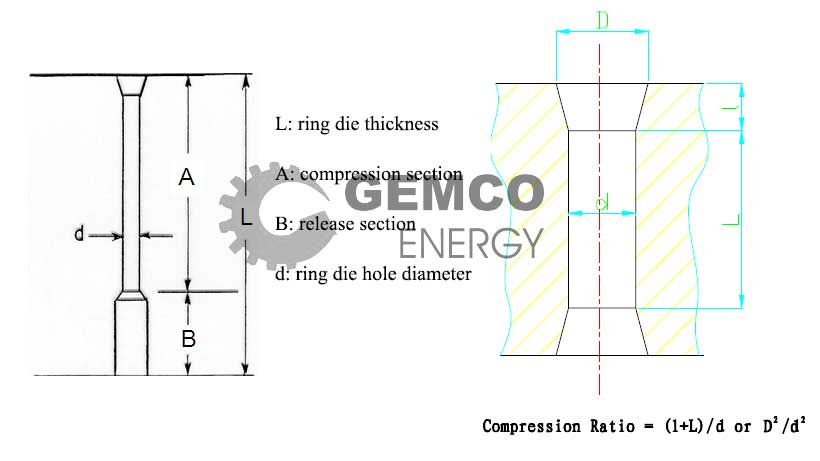
So let's talk about the compression ratio of poplar wood at 1: 6. What does one and six of the numbers represent, respectively?
The diameter of each pellet mill die hole of wood chip pellet mill machine is 6 mm / 8 mm / 10 mm. This 1 represents the diameter of each ring die pellet mill die hole. If the diameter of the pellet mill die hole is 8 mm, then this 1 represents 8.
And six represents the effective aperture, and the effective aperture is equal to the diameter of the hole multiplied by the effective aperture length. Which means 6*8=48, in other words 8:48. 8:48 was reduced to 1: 6 and 1: 6, which is the compression ratio of poplar.
The output of the sawdust pellet press machine depends on the compression ratio of the ring mold. If the customer does not have a very high molding rate to produce the sawdust pellets, please reduce the compression ratio appropriately, which can increase the output. But it can also reduce the service life of die and press wheel.
So how to choose the right ring die pellet mill ring mold?
- First of all, under the premise of selecting high quality ring die, according to the density of the raw material, we should select the appropriate die hole form, opening rate and compression ratio (compression ratio = effective length of die hole / die hole diameter).
- On the premise of ensuring the strength of ring die, the opening rate of ring die should be improved as far as possible.
- For some varieties of material, under the condition of ensuring reasonable compression ratio, sometimes, the ring die is too thin so that the ring die strength is not enough, and the explosion die phenomenon will appear in the production.
- Under the condition of ensuring the effective length of the die hole, the thickness of the ring die should be increased and the relief hole should be opened.
- The die compression ratio of the wood chip pellet making machine is the ratio of the effective length of the ring die hole to the minimum diameter of the ring die hole, and it is an index to reflect the extrusion strength of the wood pellets.
- The greater the compression ratio, the stronger the debris pellets will be squeezed out.
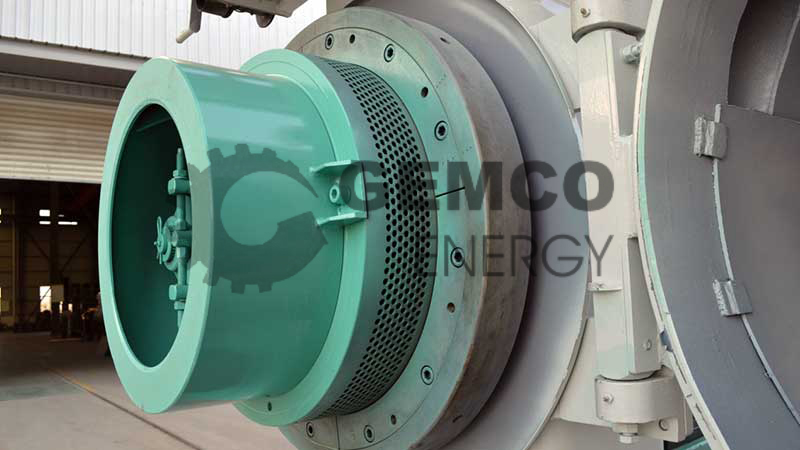
Notes:For the compression ratio of the ring mode which has straight holes, the effective length of the ring die hole is the total thickness of the ring mode, and the minimum diameter is the diameter of the die hole itself.
For the release step hole and the outer cone hole, the effective length of the die hole is the total thickness of the ring mode minus the length of the release hole or the outer cone hole, and the aperture of the small diameter section is the aperture to calculate the compression ratio.For compression step holes and inner tapered holes, this case is very special. Generally, the thickness of the whole ring die is taken as the effective length of the mold hole, and the minimum diameter is the aperture of the small diameter section.
Of course, there is a difference between the calculated ring mode compression ratio and the first two cases.
Roughness is also an important index to measure the quality of ring die pellet mill ring mold.
At the same compression ratio, the higher the roughness is, the greater the extrusion resistance of wood chip pellets will be, the more difficult the material will be formed, and the roughness of the ring die pellet mill die will also affect the quality of the surface of pellets. The appropriate roughness value should be between 0.8 and 1.6.
After reading this article, you may get a general idea of pellet mill ring mould compression ratio, and find solutions to your problems about ring die pellet mill dies. GEMCO offers quality pellet making press and free consultation. Any other questions or needs, please contact us. Thanks.